Istoria metalurgia fierului
Acasă »Istoria metalurgiei fierului
Fier. Măruntaiele planetei bogate în acest metal, care este numit pe bună dreptate „fundamentul civilizației.“ Ca în cazul în care nu la o parte cu comorile lor, natura, legat ferm de fier cu alte elemente (în principal de oxigen), l-au ascuns într-o varietate de minerale minereu. Dar, în cele mai vechi timpuri - în al doilea mileniu î.Hr. - omul a învățat pentru a extrage metalul dorit să-l.
Întreaga istorie a metalurgiei fierului, de la declanșarea topirii, gropi până în prezent, este un proces de îmbunătățire continuă pentru prepararea acestuia. Acum câteva sute de ani a existat un furnal - o mașină de înaltă performanță, în care minereul de fier se transformă în fier - materie primă pentru fabricarea oțelului. S. procesului de furnal Pori a devenit un element major al tehnologiei de producție a oțelului.
Procesul de extracție a minereului de fier în furnal făcut metalurgia istoriei intitulat „syrodutnyh“ este suflat în cuptorul ca neîncălzit - brut - aer (explozie cald a apărut pe plante metalurgice din secolul XIX, numai). Gets în syrodutnyh forja de fier sunt uneori insuficient puternice și solide, precum și articole din acestea - cuțite, topoare, sulițe - nu a rămas cot ascuțit, repede rupt în jos.
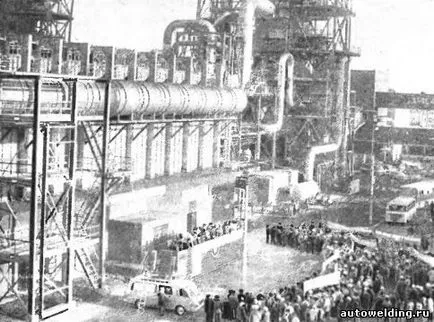
În partea de jos a vetrei, împreună cu bulgări relativ moi de fier peste si mai greu - cele care contact strâns cu cărbune. Observând acest model, oamenii au început să crească în mod deliberat o zonă de contact cu cărbunele și fierul, astfel, carboniza. Acum, metalul a fost în măsură să satisfacă cele mai exigente maestru. Era oțel - cel mai important aliaj de fier, care încă mai servește ca material structural principal.
Cererea de oțel are întotdeauna și aproape peste tot înaintea producției sale, și tehnica metalurgiei primitivă lung rămas în urma cerințelor vieții. Este surprinzător, dar timp de aproape trei milenii, fier și oțel nu sunt fundamentale nu sa schimbat - baza pentru producerea de fier și oțel pune toate același proces syrodutnyh. Cu toate acestea, dimensiunea crește treptat coarne, îmbunătățit forma lor, a crescut puterea de explozie, dar a ramas tehnologia neproductive.
În Evul Mediu a găsit un fel de corn syrodutnyh cuptor ax ajunge la o înălțime de câțiva metri. În România, aceste cuptoare numit domnitsami - de la drevnerumynskogo cuvântul „dmenie“ înseamnă „suflare“. Ei încărcați număr deja solide de materiale de încărcare - minereu de fier și cărbune, iar aerul necesar este de multe ori mai mare decât pentru coarne syrodutnyh primitive. Acum, „respira“ prin energia de apă cuptor: burduf conduse de tuburi speciale în primul rând de apă și mai târziu roți uriașe de apă.
In cuptorul cu cuvă pe unitatea de timp a fost de ardere mai mult combustibil decât în cuptor și se emit în mod natural mai multă căldură. Că temperaturi ridicate într-un cuptor și adus la faptul că o parte din fier redus, eliberat de oxigen, dar puternic carbon saturat, topit și a curs din cuptor. Anchilozare un astfel de aliaj fier-carbon care conțin de câteva ori mai mult carbon decât oțelul, devenind foarte greu, dar foarte fragil. Era fierul.
Rolul său în dezvoltarea industriei este foarte importantă, dar cu câteva secole în urmă, afaceri de master de fier a avut loc o opinie destul de diferit; deoarece acest metal sub loviturile ciocanului sfărâmă în bucăți, și să-l o arma sau o unealta a fost pur și simplu imposibil. În același timp, din aceasta cauza, indiferent de suma nu este aliaj potrivit unui produs bun - fier Kritsa - a redus drastic.
Pur și simplu nu s-au dat metalurgiști medievale porecle noi din aliaj. În Europa Centrală, a fost numit o piatră sălbatică, gâscă, Anglia - fier swinish (fier în limba engleză este numele acum), iar cuvântul rusesc pentru porci, adică lingouri de fier are aceeași origine.
Deoarece nici o cerere de fier nu a fost găsit, este de obicei aruncată într-un depozit de deșeuri. Dar, în secolul H1U, cineva a avut gândul fericit înapoi pentru a încărca de fier în cuptor și topit împreună cu minereul. Această încercare a marcat o adevărată revoluție în industria fierului și oțelului. Sa dovedit că această metodă face relativ ușor pentru a obține oțelul dorit, de altfel, în cantități mari. Din păcate, istoria nu a păstrat pentru noi numele acestui inventator medieval.
Această inovație a dus la o separare clară a „muncii“: în domnitsah, devenit deja de timp mai avansate furnale, de minereu topit fier de porc, și podoabe din acestea elimină excesul de carbon, care se realizează procesul de conversie a fontei în oțel - „redistribuire bloomery“ . Deci, a existat un proces în două etape pentru producerea oțelului din minereu de fier: minereu - fier, fier - oțel.
Acum, cererea de fier, mai ales ca intermediar, este apoi convertit în oțel, a crescut dramatic. Și furnale au aparut peste tot ca ciupercile după ploaie. Dar, ca și pentru furnalul necesară o mulțime de cărbune, în curând în acele țări care nu erau bogate în păduri, el a început să fie simțit acut lipsa acesteia, și metalurgie, lipsit de combustibil, a fost aici în declin. Acest lucru sa întâmplat, de exemplu, în Anglia, a ocupat mult timp poziții de lider în producția de fier.
Situația dificilă, care a fost în legătură cu industria britanică a forțat steelmakers să solicite înlocuirea cărbune. În primul rând, atenția lor a fost atrasă de cărbune, care natura, fără restrîngerea, a dat Insulele Britanice. Cu toate acestea, toate încercările de fier mirosit pe ea au eșuat: cărbunele în timpul procesului de încălzire a fost de la sol, iar acest lucru a împiedicat foarte mult explozia. Dar, în final, în 1735, englezul Abraham Derby a reușit în cocs de furnal - combustibil produs din cărbune cocsificabil când este încălzit fără accesul aerului la temperaturi ridicate (950-1050 ° C), iar cărbunele nu este măcinat și sinterizate în bucăți . Astăzi, fără cocs sau furnal de topire de neconceput, nici un număr de alte procese metalurgice.
XVIII-lea si al XIX-lea a adus o mulțime de noi construcții în furnal a fost inventat prima mașină-suflare a aerului, și lângă furnalul sus „garda de onoare“ - un imens trabucuri boante sobe, datorită cărora cuptorul este acum aer cald este furnizat.
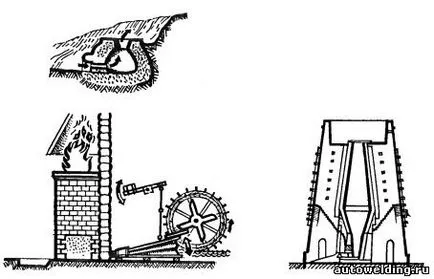
forja pentru fier antic Kritsa.
Cornul de suflare a aerului (secolul al XVI-lea). Furnalului (sfârșitul secolului al XVIII)
Apoi, în istoria metalurgiei a fost scrisă o altă pagină importantă: proiectat cuptor cu arc electric, permite obtinerea de metal de înaltă calitate. În flăcări, mii de ani de deținut în mod exclusiv toate drepturile pentru topirea metalelor, un concurent serios - un curent electric.
În ultimele decenii, industria există un fel de „accelerare“: dimensiunea diferitelor cuptoare sunt în creștere de la an la an. Cât timp au explozie focar de două mii de metri cubi este considerat aproape o minune a lumii, iar astăzi este mult mai impresionant colos din lume - „cinci mii de metri“, „patru-thousander“ și chiar
Într-o altă perioadă lungă de furnal menține cu siguranță valoarea sa. Cu toate acestea, soarta lor este greu de senină. Spre deosebire de vatra primitivă antic în care strămoșii noștri preparate de fier direct din minereu, moderne structura gigantica - Furnalelor - produce cea mai mare parte nu metalul care a necesitat direct tehnica, dar numai produsul de porc este convertit apoi în etapa următoare ne dorit oțel (o excepție este din fonta care se extinde în producția de piese turnate, proporția este mai mică de 15 la sută într-un volum total de fontă topită). Cu alte cuvinte, într-un efort de a atinge steelmakers cantitative ridicate sunt nevoiți să meargă așa cum au fost, într-un mod sens giratoriu.
Problema schimbării fluxului de proces în fabricarea oțelului a fost mult timp oamenii de știință. Și nu este la dorința de mers în gol pentru a îndrepta calea industriei oțelului rutier. Motivul este diferit.
În furnal are un dezavantaj serios. Esența este că, chiar dacă poate părea la prima vedere pare ciudat că un necesar „fel de mâncare“ în dieta ei - cocs. Același cocs, invenția care a fost un punct de referință în dezvoltarea metalurgiei fierului. La urma urmei, este datorită cocs pentru două și un cuptor de secole și jumătate explozie devine un excelent high-calorii „alimente.“ Dar, treptat, orizontul explozie a început să apară nori, care poate fi numit în mod justificat o cola.
În natura cocs, după cum știm, nr. Este derivat din combustibili fosili. Dar nu toate. Și numai unul dintre cei care sunt predispuse la cocsificare (sinterizare). în lumea de cărbune nu este foarte mult, astfel încât în fiecare an, acestea sunt din ce în ce mai rare și mai scumpe. Și încă mai trebuie să transforme cărbune în cocs. Acest proces este destul de complicată și consumatoare de timp, însoțită de eliberarea de dăunătoare produselor secundare nu sunt arome de parfum. Pentru a elimina posibilitatea de a le atmosferă, apă, sol, este necesar să se construiască dispozitive de tratare a apei scumpe.
Creștere a prețului de cocs a condus la faptul că el a fost articolele cele mai solide din costul de fier: reprezintă aproximativ jumătate din toate costurile. Acesta este motivul pentru care furnalului în mod constant să depună eforturi pentru a reduce consumul de cocs, parțial înlocuirea acestuia cu gaze naturale, cărbune pulverizat, păcură, și aici este deja realizat un succes considerabil. Deci, probabil, în curs de dezvoltare ofensiva pe cocs, furnal, treptat, capabil să scape complet de ea? Dar atunci trebuie să scapi de ea însăși și prin furnale: cocs, deoarece fără ea, că cuptorul fără foc.
Industria Probleme cokeless ia un alt fondator al metalurgiei moderne DK Cernov. La sfârșitul secolului trecut, el a propus un design original al cuptorului cu cuvă, care nu ar fi topit fontă și fier și oțel. Din păcate, ideea lui nu a fost destinat să fie realizat. După aproximativ un deceniu și jumătate după Cernov a prezentat proiectul său, el a scris cu amărăciune: „Ca urmare a inerției obișnuită de fabricile noastre particulare, am apelat la Ministerul Comerțului și Industriei, în speranța de a fi în măsură să pună în aplicare metoda propusă într-o formă simplificată într-una din plantele miniere de stat. Cu toate acestea, în ciuda dublu marcat de atunci ministrul dorința de a ajuta la producerea unei astfel de experiențe, întrebarea este îndeplinită obstacole de netrecut între dulapurile și coridoarele Ministerului. "
producție Susținător bezdomennogo a fost și D. I. Mendeleev. „Cred - a scris la începutul secolului - care va veni cu timpul din nou, timp să caute modalități de a direcționa producția de fier și oțel de minereu, care trec fierul.“
Timp de decenii, oamenii de știință și ingineri din diferite țări au încercat să găsească o DRI tehnologie acceptabilă. au fost emise sute de brevete, a propus și a dezvoltat diverse ansambluri, instalarea cuptorului. Cu toate acestea, chiar și cele mai aparent promitatoare idei pentru o lungă perioadă de timp nu a fost posibil să se pună în aplicare.
Un pas important în dezvoltarea tehnologiei directe de fier a fost făcută în anul 1918, când inginerul suedez M. Viberg sugerat proces de reducere de plumb în cuptorul cu cuvă, folosind în acest scop un gaz combustibil care conține monoxid de carbon și hidrogen. O metodă de conversie a minereului de fier, pentru a permite 95 de procente de fier. Dar (și nu a fost fără un „dar“), în acest fel a fost un dezavantaj major: materia primă pentru reducerea gazelor care deservesc toate același cocs, și pentru gazeificarea nevoie de dispozitive complexe și costisitoare - elektrogazogeneratory.
În țara noastră, un mare pasionat de tehnologie bezdomennoy a fost profesor asociat al Institutului Siberian metalurgic VP Remin. La sfârșitul anilor 30-e el a dezvoltat o structură electrică în care minereul a fost topit, alunecare pe o vatră înclinată, ca gheața în munți (așa numitele cuptor glacial), și apoi prin topire presupus recuperarea fierului. Atacul trădătoare țara noastră, Germania nazistă a stabilit metalurgiștilor multe provocări, iar aceste experimente a trebuit să fie amânată până la vremuri mai bune.
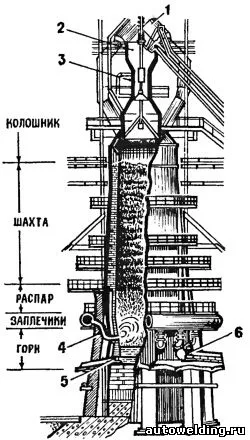
Furnalului: 1 - bena; 2 - receptie buncăr 3 - distribuitor lot 4 - lance aer; Lotka fier - 5: 6 - zgură Lotka.
Dar când au sosit, sa dovedit că experții nu au un singur punct de vedere. Unii necondiționat numit de secole dovedite de furnal, în timp ce alții au văzut bezdomennye cokeless și perspective. În 1958, Academicianul I. P. Bardin, comentând fierul direct din minereu, a remarcat că „bine-cunoscut metalurgist american Smith, care a numit piatră de moară furnalului atârnat în jurul gâtului și oțel lui ca o pedeapsă pentru păcatele sale în domeniul cercetării a trebuit să atunci când se analizează procese specifice merge înapoi în furnal ca o singură unitate în momentul în care se poate baza de metale. "
În acei ani, industria metalurgică și într-adevăr nu au avut o alternativă utilă în furnal. În ciuda numeroaselor încercări de a dezvolta metode de producere a fierului direct din minereu, găsi o soluție care să satisfacă metalurgiștilor necondiționat, timp îndelungat, fără succes. Sau imperfectă a fost schema tehnologică, fie fragile sau neproductivă echipamente exercitate sau lăsat mult de dorit calitatea metalului. În plus, opțiunea propusă este de multe ori nu se justifică economic: metalul devine foarte scump. A rămas dificilă și alegerea agentului de reducere. Rețeaua de căutare a stagnat în timp ce Suedia, URSS, Statele Unite ale Americii. Mexic, Venezuela, Germania și Japonia au fost mai multe plante mici pentru producerea directă a minereului de fier.
Faptul că aceste țări înainte ca ceilalți au început să pună în aplicare o nouă tehnologie, nu a fost surprinzător. De exemplu, în Suedia, metalurgie sa specializat mult timp în producția de oțel inoxidabil, și, după cum experiența a arătat, modul de reducere directă - aceasta este calea de urmat pentru a îmbunătăți calitatea metalului. Liderii În ceea ce privește Mexic și Venezuela, acestea au devenit refractari - în aceste țări există cărbune cocsificabil, dar există rezerve mari de gaze naturale, astfel încât dezvolta industria fierului si otelului pe baza, adică furnale construirea tradiționale, acestea ar putea să nu, dacă au vrut să.
Până la sfârșitul metalurgiști cele 50 au ajuns la convingerea fermă că rolul agentului de reducere în procesul de fier directe ar trebui să acționeze cu gaz. Acest lucru a însemnat că cercetări suplimentare ar trebui să se desfășoare în direcția sugerată Wiberg. Curând, în unele țări, au fost găsite soluții de succes. Astfel, un avantaj al tehnologiei propuse a fost aceea că agentul reducător are practic liber: inventatorii au propus utilizarea degazată magazine EAF in care sunt eliberate în atmosferă, înainte. Original a fost o altă soluție. Dintr-un cuptor cu cuvă, în care fierul este redus, gazul fierbinte este direcționat nu spre cer, și în schimbătorul de căldură și livrat căldura la gazul de intrare pentru agentul de reducere.
Valentin Semenovich Kudryavtsev.