Mel White pigmenți coloranți ciment microcalcite
intrare
Evacuate de la sfârșitul secolului trecut silicat caramida a devenit în multe părți ale materialului de construcție favorit din lume. În Europa, cărămida silicat este produsă în cantități mari, în principal în Germania și Țările de Jos. Anglia, Elveția. Danemarca și Suedia. Ponderea majoră a producției este în blocuri și cărămizi perforate utilizate pentru construcția pereților și a partițiilor exterioare portante. Cu caz ca cărămizi silicat de calciu poate fi, de asemenea, utilizat cu mare succes ca o cărămidă pentru zidărie din față netedă. Împreună cu corpolent Cărămida de silicat având o suprafață netedă adesea servește ca o cărămidă așa-numita zdrobit cu o suprafață în chip carieră de piatră zidărie. ashlaring netedă și chiar mai ambreiaj de caramida de siliciu zdrobit efect arhitectural distinctiv. Acest efect este amplificat de posibilitatea de a utiliza caramida de siliciu colorat. În acest scop, astăzi sunt pigmenți anorganici (coloranți), care asigură în mod fiabil o colorație stabilă de cărămidă de siliciu. Ashlaring cărămizi de silicat pictate, uneori, deja în uz, se subliniază capacitățile multilaterale ale acestui material.
Conform rezultatelor cercetării încă colorat stabil cărămizi silicat pot fi furnizate numai în cazul în care. când întreaga greutate var-nisip colorat pigment respectiv (colorant). Suprafața Paint - indiferent de compoziția de cerneală - poate înlocui rezistența la pătare și greutate. în plus, se închide structura caracteristică de cărămidă de siliciu.
Pigmenții utilizați trebuie să îndeplinească următoarele cerințe:
- rezistență la acțiunea varului
- rezistenta la temperaturi ce apar în timpul solidificării cărămizi
- lumina si intemperii, ca culoare cărămizie nisip-var trebuie să păstreze culoarea lor bine atunci când sunt utilizate pentru zidarii exterioare.
Studiile au arătat că, în plus față de pigmenți organici (coloranți). care nu sunt potrivite pentru vopsirea caramida de siliciu din cauza slabei rezistențe alcaline sau lumină insuficientă și weatherability, precum și anumiți pigmenți anorganici (coloranți) sunt improprii pentru acest scop.
Următoarele produse din gama de pigmenți anorganici Bayferrox® în întregime adecvați pentru producția de cărămizi de silice:
Red toate tipurile roșii Bayferrox®
Galben galben toate tipurile de Bayferrox® Colortherm 3950
Brown „Bayferrox®645 T
Negru Bayferrox® 303 T
Green Chromoxidgrun (oxid verde de crom) GX. GN
* Prin amestecarea pigment roșu și galben Bayferrox® 303 pigment Bayferrox® T pot primi diferite nuanțe de maro
După cum se poate observa din lista de mai sus, cele mai multe dintre pigmenții negru și maro Bayferrox6 nu a fost inclusă în această listă. Acest lucru se datorează faptului că, ca urmare a oxidării pigment negru BayFerrox ^ suferă schimbare de culoare în abur, în direcția de roșu-brun și este, prin urmare, nepotrivit. Pe de o parte, acest lucru se aplică tipurilor maro, deoarece acestea pot fi obținute prin amestecarea pigmenților roșu și galben și / sau negru (coloranți) Bayferrox®. Pe de altă parte, pigment galben BayFerrox, deși la expunerea la temperatură normală (> 43 180), de asemenea, supuse modificări de culoare în direcția roșie, sunt stabile în timpul abur. Acest lucru se datorează dispun de procesul de întărire prin abur. care constă în faptul că, chiar și atunci când aburul la 16 bar (204 „C) sunt legați chimic de apă în pigment galben BayFerrox * nu scindat.
Introducerea pigment în producția de cărămizi de silice
Atunci când se analizează producția de cărămidă de siliciu ridică problema pigment când și unde în procesul de producție este administrat cel mai bine (colorant). Aceasta depinde de tehnologia de producție aplicată la fabrica. În principiu, folosesc atât tehnologia de amestecare în masă continuă și periodică var-nisip. De obicei, au tendința de a introduce un pigment (colorant) al reactorului, reactorul este liber de vopsea. Dar acest lucru este posibil numai în cazul în care mixer poslevklyuchenny asigură o amestecare intensivă a pigmentului (colorantul) de la sol. pigmenți foarte fine (coloranți) nu pot fi distribuite în întregime în masa de var-nisip relativ uscat la eficiență amestecare insuficientă. Prin urmare, de mare putere de colorare de pigmenți (coloranți) utilizat incomplet și, în plus, se pot forma pete colorate nedorite.
În lot tehnologie recomandată obligatoriu intensivă mixer dacă pigment (colorant) care trebuie administrat după reactor. Mai mult, este cunoscut faptul că amestecarea intensivă îmbunătățește calitatea cărămizii ulterioare. Într-un proces continuu utilizând un amestecătoare dublu ax cele mai multe cazuri, imposibil de a oferi o distribuție bună a pigmentului în mixer poslevklyuchennom. pigment Prin urmare, într-un proces continuu care trebuie administrat (colorant) în amestecător amonte trebuie să se supună pigment ar putea dubla procesul de amestecare. Mai mult, șederea în masă de var-nisip în favorurile reactoare de amestecare cu masa de pigment în mixer poslevklyuchennom. Datorită proprietăților de curgere relativ sărace de pigmenți sub formă de praf necesare în acest caz de dozare continuă a pigmentului duce la probleme în cazul în care o precizie de dozare trebuie să îndeplinească cerințe stricte. Aceste două probleme - dozare continuă curentă de pulbere sau suspensie apoasă de pigmenți și o bună amestecare - pot fi acum rezolvate cu ușurință folosind dozatoare moderne și dispersanți. Cu toate acestea, atunci când intră în suspensia apoasă trebuie să se considere că gradul de pigmentare este limitat, și anume, faptul că numai cantități limitate pot fi administrate pentru reglarea umidității de turnare.
Utilizarea de pigment granular nu este potrivit pentru producerea de cărămizi de silice. Acest lucru se datorează faptului că, în contrast cu pietrele de pavaj de beton distribuția granulei în amestecul de var-nisip fin necesită mult mai mult timp și energie de dispersie și, în cele din urmă încă cauzează probleme. Dacă, în ciuda acestor pigmenți granulare, datorită avantajelor lor incontestabile în continuare sunt de interes, trebuie să efectueze mai întâi teste de la fabrică.
Dependența nuanța cantității de pigmenți și alți factori
a) Cantitatea de pigment (colorant)
Proporția de pigment este cel mai bine determinată în procente de greutate raportat la greutatea totală a nisipului și var, indiferent dacă pigmentul este introdus ca o pulbere uscată sau o suspensie apoasă. Deoarece caramida silicat în cele mai multe cazuri, are doar propria culoare de lumină, puteți produce cu ușurință un nisip-var culoare variază de cărămidă de la nuanțe pastelate la culori intense, dar din cauza culorii luminii nu se poate obține propria lor culoare intensă de cărămizi de lut. Mai jos sunt repere cantitatea necesară de pigment (ca procent în raport cu greutatea totală):
Pastel culori 0.2-0.5% pigment
Nuante de intensitatea medie de 0,5 -1% pigment
ton Intensive 1 - 2% din pigment
Ca și în cazul altor materiale de constructii de colorat, cum ar fi beton, ipsos, mortar, etc. în cazul caramida de siliciu, se observă că creșterea procentuală intensitatea culorii scade odată cu creșterea aditiv pigment. și anume există o limită așa-numita saturație. Fig. 1, de exemplu, Bayferrox® 920 pigment (galben) prezintă creșterea intensității culorii în funcție de cantitatea de injectare a pigmentului. Măsurătorile au fost efectuate pe probe colorimetru corespunzator pigmentate care au fost fierte 8 ore la 8 bar. Rezultă că, în intervalul 0 - creșterea cu 1% în intensitatea culorii pigmentului este mult mai mare decât în intervalul de 1 - 2% pigment.
Culoare cărămizi silicat este determinată în principal de nisip de culoare proprii utilizate ca var - cu câteva excepții - are o culoare albă, care variază doar ușor. Deoarece, în conformitate cu rezultatele examinării microscopice a pigmentului este fixat în liant, care nu este complet învelește boabele de nisip, nuanța rezultată depinde în mare măsură pe cont propriu de nisip de culoare.
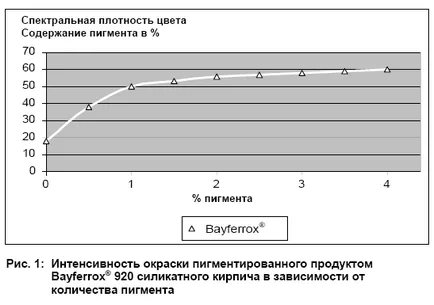
Este ușor de înțeles că această culoare proprie joacă un rol mai important decât mai puțin aditiv de pigment. De obicei, nisipul utilizat în cărămizi industria silicat are o culoare brună mai mult sau mai puțin intensă, în funcție de cea mai mare parte de conținutul de oxid de fier. De aceea, odată cu creșterea intensității de culoare schimbări de nuanță nisip natural, de exemplu, galben - în direcția de o nuanță mai închisă, mai murdar, cu roșu - în direcția unei albăstrui-roșu, în timp ce verde - în direcția de o culoare verde-albastru murdar. De aceea, nu trebuie să uităm că producția de cărămidă de siliciu colorate uniform pentru o lungă perioadă de timp este asociat cu anumite dificultăți, deoarece chiar și nisipul din aceeași carieră nu au întotdeauna aceeași culoare. Prin urmare, în plus față de alți factori care sunt cunoscute de a afecta culoarea de cărămizi nisip-var în funcție de nisip, este necesar în producția de cărămidă nisip-var colorat și să acorde o atenție la propria culoare de nisip, pentru a evita fluctuațiile prea mari în producția de nuanțe. Pe de altă parte, o anumită, nu prea masiv nuanțare poate avea o influență pozitivă asupra aspectului zidăriei feței.
Întotdeauna vine de la faptul că, odată cu creșterea conținutului de oxid de calciu în amestecul devine nuanta mai deschisa, cu un conținut neschimbat de pigment. Prin urmare, este interesant să se cunoască măsura în care fluctuațiile de conținut de var tehnologic condiționat poate duce la un efect marcant asupra nuanța care rezultă din cărămidă de siliciu. Cu toate acestea, experimentele corespunzătoare au arătat că acest lucru se întâmplă atunci când fluctuații relativ mari în conținutul de var. Discrepanțele var conținut de aproximativ ± 1%, cu aproape nici un efect asupra nuanței rezultat.
d) condițiile de solidificare
un impact semnificativ mai mare asupra condițiilor de solidificare care oferă umbră. Experimentele noastre au arătat că, odată cu creșterea presiunii pereche de culoare sunt mult mai pală. Condițiile de testare au fost modificate în intervalul de 8 - 16 bar. timpul de solidificare derivată și presiunea aburului a fost astfel, în fiecare caz, 64 bar * h. Condițiile de solidificare cel mai des întâlnite cuprind 8 ore la 8 bar și 4 ore la 16 bar. caramida de siliciu pigmentată, care se solidifică în aceste condiții aburinde, caracterizate prin același număr de nuanțe de diferențe clare de pigment, și anume în sensul că umbrește cărămizi, aburit la 16 bar sunt mai palide decât în cazul cărămizilor, aburit la 8 bar. Deoarece este posibil să se elimine reacția dintre var și pigment. Acest efect de albire trebuie explicate prin formarea diferitelor produse de reacție și cantitatea de liant în reacția dintre oxid de calciu și acid nisip de siliciu. Lucru este. că efectul luminarea a fost observată în cărămizi nepigmentate așa cum a fost posibil să se stabilească prin măsurarea luminozității cărămizi silicat în aceste condiții. Efectul descris aici se produce nu numai în experimentele de laborator, dar, de asemenea, a jucat bine în testarea producției respective. Se poate trage concluzia că pentru o intensitate maximă de culoare pentru o anumită cantitate de pigment condiția preferată pentru producerea de caramida de siliciu este abur la 8 bar.
Durabilitate caramida de siliciu pigmentat
Pentru producătorul de caramida de siliciu este important să se cunoască modul în care puterea de cărămizi de silicat poate varia în funcție de aditivul pigment. Pentru a clarifica această întrebare prisme au fost fabricate din amestec de var-nisip 16 x 4 x 4 cm, în care proporția de pigment a fost crescut la 4% în greutate - bazat pe total, adică la o sumă care aproape niciodată nu este utilizat. Prisme aburit 8 ore la 8 bar și la 24 de ore pentru a testa rezistența lor și la încovoiere la tracțiune de compresiune. Fig. 2 și 3 prezintă rezultatele testelor efectuate cu pigmenți BayFerrox * 110 (roșu), Bayferrox6 „920 (galben) și Chromoxidgrun (oxid de crom verde) GN. Rezultatele arată că puterea nu este redusă chiar și la adăugări extrem de ridicate de pigmenți.
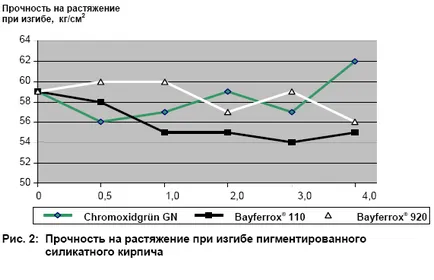
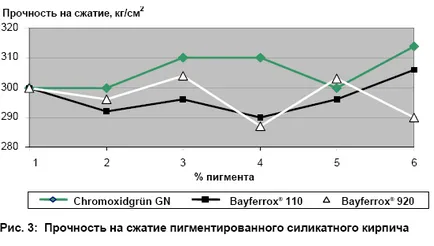
silice Limpezirea dioxid de titan cărămidă
In concluzie, aceasta ar trebui să indice, de asemenea, posibilitatea de deschidere a culorii caramida silicat prin adăugarea de dioxid de titan, așa cum este practicată pe scară largă pentru a crește albeaa cimentului alb umed. Dintre numeroasele tipuri disponibile pe piață în acest scop sa dovedit a fi complet adecvat prime de tip anatas, la fel ca în acest caz, de tip rutil nu oferă nici un avantaj și, de asemenea, prea scump. albeață absolută obținută prin adăugarea de dioxid de titan, desigur, depinde de albeața inițială a materiilor prime utilizate. Acest alb inițial este determinat, după cum sa menționat deja, utilizate în principal culoarea lor de nisip. Oricum, deja o mică adăugare de dioxid de titan conduce la o albire marcată, în special atunci când cărămizi umede. Ca cu adaos de pigmenți colorați cu decolorant dioxid de titan, există o scădere semnificativă în creșterea procentuală cu cantități crescute de pigment. Performanța cea mai rentabilă este atins atunci când cantitatea de pigment la 0,5 la 2%.